In Commercial Diving, safety is non-negotiable. Recently, Unique Group conducted a thorough audit and service of a competitor’s air diving system, highlighting the vital importance of prioritising quality over cost when it comes to diving equipment. We take a closer look at what we found and why it matters for the safety of everyone involved in Commercial Diving operations.
Pressure Vessel Manufacturing and Testing
Our audit uncovered some issues in the pressure vessel manufacturing and testing process.
- Lack of weld fusion and undercuts in certain areas were found.
- The report on the pressure vessel’s hydrostatic test did not mention if the medical lock was included as part of the test.
- Critical PVHO documents including post hydro testing NDT were missing from the chamber manufacturing data book.
The lack of these documents emphasizes the need for robust manufacturing quality plans and thorough testing, ensuring that every detail is accounted for to meet the required standards.
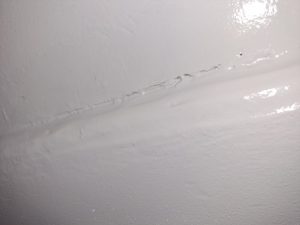
Dive Control Communication Units & Relief Valves
It was noted the communication units in the dive control system were not suitable. They were portable units, removed from transit cases and mounted in a way that exposed their electronic parts to harsh marine conditions.
This could lead to corrosion and equipment failure, underlining the importance of choosing the correct OEM equipment that can withstand the marine environment. Certain relief valves on the control panel were fitted after the gauge, in the event of an over pressurisation the gauges could be damaged or fail.
Machinery Van Safety Measures
In the machinery van, there were no circuit breakers for high-pressure and low-pressure compressors, with only isolation switches fitted.
Container Modifications and Material Selection
Areas, where modifications were made to containers, lacked the correct painting process, resulting in the development of rust where modifications had taken place. In the marine environment, where rust is common, following the right procedures for surface protection is vital.
Additionally, the materials used in certain parts of the launch and recovery system were not suitable for the harsh marine conditions. This highlights the need for choosing materials and paint specifications that can withstand marine environments.
Launch and Recovery System Design
The design of the emergency braking system in the launch and recovery setup raised safety concerns. It’s manually activated, meaning if the main brake fails, the operator could be placed in the line of fire. The positioning of control boxes makes it difficult for the winch operator to see the hydraulic system status.
Adding to that, there’s no emergency changeover valve on the hydraulic power system, and some hydraulic piping isn’t properly protected using Denso Tape or similar method of protection. It was also noted that the A-frame structure was not fitted with a wire catcher which safeguards the uncontrolled descent of the basket in the event of a sheave wheel failure.
Conclusion
In conclusion, our recent audit reinforces the need to prioritize quality over cost when it comes to diving equipment. While saving money may be tempting, compromising on the quality of gear can lead to serious safety issues and operational downtime. As a leader in the industry, Unique Group is committed to utilising proven designs, and the highest quality materials and components. Putting safety and reliability before cost.
If you are looking for a commercial diving equipment, connect with our Unique Group technical specialist and we can provide you expert advise on choosing the right system for your needs and even manufacture the system for you with the best industry standards. Explore the range here.